Research on Energy-saving Technology of the Rolling Process
Steel rolling energy saving has a great impact on steel rolling production, especially in our country, the energy consumption is huge, so it is urgent to improve the energy-saving technology of production process. At present, the development of steel rolling technology in Lulei is also based on energy saving. New technology, process, and equipment of steel rolling are emerging constantly. The energy-saving effect is adjusted and the energy consumption of the process is reduced by changing the coefficient of each process in steel rolling production. This paper analyzes the energy-saving technology of the Lulei steel rolling process.
About 12% of the total energy consumption of the whole country is the energy consumption of the iron and steel industry, while the energy consumption of steel rolling accounts for about 15% of the energy consumption of iron and steel. At the same time, due to the continuous improvement of the quality of steel, the energy consumption of steel rolling is still increasing. Based on this, energy conservation and emission reduction of the steel rolling production process are of great significance to reduce energy consumption and pollution. In terms of current energy and ecological environment, the concept of energy conservation and emission reduction must be put into practice.
Current Situation of Steel Rolling Production
China is a large country of production and manufacturing, and the iron and steel industry accounts for an important proportion. With the expansion of the iron and steel industry, energy consumption is increasing day by day. According to incomplete data, the energy consumption of the iron and steel industry accounts for about 13% of the world's total energy consumption, while the energy consumption in steel rolling production process accounts for 15% - 20% of the total energy consumption of China's iron and steel industry. With the expansion of all walks of life, the types of steel products are increasing, and the total demand is also increasing. At the same time, the rolling process is becoming more and more complex. The relevant research shows that the energy consumption of cold rolling and hot rolling processes in China is significantly higher than that of foreign steel rolling processes. Compared with foreign advanced technology, China's rolling technology, management technology, and related equipment are still relatively backward. At present, steel rolling equipment is the main energy consumption equipment in China's iron and steel production. Its energy consumption accounts for about 70% in the whole steel rolling system. Therefore, it can be seen that China's steel rolling production also contains great energy-saving potential.
Analysis of Factors Affecting Energy Consumption in the Rolling Process
1. Effect of heating temperature. The energy consumption of the rolling process mainly includes fuel energy consumption, power equipment energy consumption, and oxidation burning loss. Although there are many factors influencing the energy consumption of the rolling process in rolling production, the heating temperature is an important factor. According to the investigation, single heat consumption has a great relationship with the billet heating temperature. When the heating temperature is between 1150 ℃ and 1250 ℃, the heating temperature is between 1150 ℃ and 1250 ℃ Within the range of ℃, the unit heat consumption will decrease when the temperature drops by 10 ℃. Therefore, to properly reduce the heating temperature, not only to ensure the normal production of billet, but also to reduce energy consumption. However, there is a linear relationship between the heating temperature and the unit power consumption, but it has little effect on the power consumption, but reducing the heating temperature can still effectively save the power consumption.
2. The thermal efficiency of the rolling furnace. The heating mode and internal structure of the steel rolling furnace are also one of the main factors affecting energy consumption. A good heating mode of steel rolling furnace can effectively improve the combustion efficiency of fuel, and more heat is generated per unit fuel. In addition, the internal structure of the furnace, especially the good lining structure, can effectively improve the heat preservation effect of the furnace and reduce the heat loss.
3. Influence of steel production mode. The heating process, temperature, and time of different steel grades are different. In the process of production, the consumption of fuel is also different. If the production process of steel grades is not used properly, not only the ideal rolling effect can not be achieved, but also the consumption of additional energy is caused. This is one of the key points of energy saving in the rolling production process.
Energy-saving Technology of Lulei Steel Rolling Process
1. Wire energy-saving technology. First, the cooling technology of the air cooling line is energy-saving. The imported high-quality high-speed wire production lines all adopt the whole closed-loop cooling system. At the same time, the spinning temperature is gradually reduced, and the product performance and uniformity are improved. The total length of the air cooling line tends to be longer, and the insulation section is longer. In order to improve the cooling rate, some enterprises began to try to reduce the wind temperature, water mist cooling and other ways to improve the cooling rate. In the annealing furnace, the hot-rolled wire rod is treated by on-line solid solution treatment. After being spun into continuous coils, the hot-rolled wire rod is cooled after holding for about 5min. The equipment investment is high, the final grain size can be controlled, and the austenitic and ferritic stainless steel can be treated. The product quality is equivalent to the traditional off-line solid solution treatment. After the hot rolling wire is spun, the fan and water mist are used in the air cooling line to improve the heat exchange efficiency and increase the wire cooling rate. High-speed pulse airflow generated by the infrasonic wave is also used to cool wire rod, which can accelerate heat transfer between wire rod and surrounding air and obtain high cooling rate. The second is the collection and packaging of energy-saving products.
The collecting drum is a kind of high-speed wire that is wound in a circle and transported by an air-cooled roller table. When the coil is transported to the opening of the collecting drum through the roller table, it falls into the collecting drum in a parabolic shape at a certain initial speed and is sheathed on the nose cone held by the supporting claw in the center of the collecting drum. The packaging process is the last process of wire packing, which has a great influence on the appearance of products. When the tangent velocity at the exit of the wire rod is not equal to that at the exit of the spinneret, and the coil falling point deviates to one side, the phenomenon of uneven coil distribution and left and right position caused by the velocity can be partially offset by adjusting the claw under the spinneret. And reasonably adjust the tray running speed to strictly ensure the coiling in the drum. In this way, due to the small falling space, the coil is always in the middle of the mandrel and the cylinder wall when falling, avoiding the occurrence of a staggered layer.
2. The steel rolling process accounts for a considerable proportion of the energy consumption in the whole country, which also indicates that the steel rolling process has a great space for energy conservation, and reducing the energy consumption of the steel rolling process will surely bring China's industrial production into a new era. All in all, in order to reduce the energy consumption of steel rolling technology and achieve the purpose of energy saving, we can mainly explore new steel rolling technology, research new steel rolling technology, and replace advanced equipment from three aspects. Through the improvement of these three aspects, we can achieve the purpose of energy saving of steel rolling technology to a large extent. In addition, we should not only pay attention to these three aspects but also start from every step of the rolling process, strictly limit the energy consumption to avoid excessive loss of energy. All in all, the energy-saving of the rolling process is a necessary project now, which has a great influence on the development of the industry. All in all, in order to achieve the goal of energy saving in the rolling process, it is necessary to explore new rolling technology, innovate the rolling process, introduce more advanced rolling equipment, and do a good job in the control of energy consumption in every step of rolling. Only by strictly controlling the rolling process can the goal of energy saving in the rolling process be achieved to the maximum extent.
3. Optimize the production process. Optimization of the production process can greatly improve the production efficiency, but also save a lot of energy, improve the heat utilization of the hot billet. In the production process of steel rolling, the corresponding production process shall be set according to different steel grades, order batches, hot billet connection, and equipment conditions to give full play to the energy-saving effect of hot charging and formulate the basic principle of furnace charging. First, when a certain amount of high-grade hot billet is in the stockyard, the furnace charging shall be arranged immediately. At the same time, in the process of furnace charging, the number of continuous blocks of medium cooling and hot billet shall be as large as possible and as small as possible In addition, scientific heating time should be established to meet the production needs of different requirements of steel grades, and the connection between heating time and different grades of hot billets should be maintained.
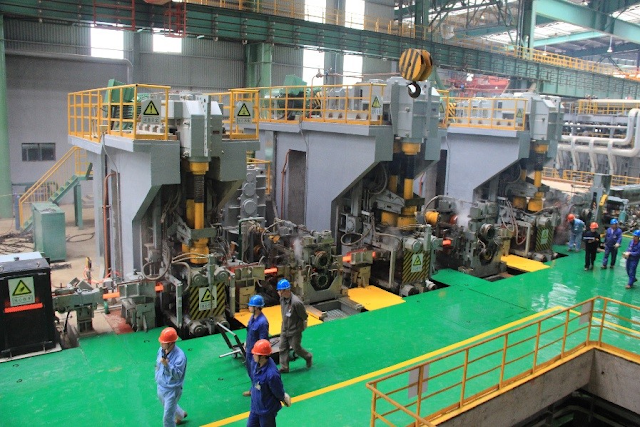
4. Properly reduce the heating temperature of billet. The results show that reducing the heating temperature of billet to a certain extent can effectively save heat energy, electric energy, and steel oxidation loss. Generally speaking, there are three control stages in the heating furnace. The heating temperature and section temperature difference when the billet is discharged is the coupling results of the actual parameters control in each stage. In order to introduce the unknown coupling results in different stages, the heating temperature should be reduced by 30 to 40 ℃ according to different steel types and specifications. In addition, the heating time and temperature should be shortened for the hot billets with temperature more than 300 ℃, and the comprehensive energy-saving effect can be achieved by reducing the heating temperature.
5. Low temperature rolling and rolling process lubrication technology. Low temperature rolling technology is an important energy-saving measure to reduce the process energy consumption of the rolling system. Reducing the tapping temperature of the reheating furnace can reduce fuel consumption, but its deformation resistance and rolling power increase. In recent years, the practical experience of many rolling productions has proved that the energy-saving effect of reducing fuel consumption is more significant. When the temperature is 1100 ℃, the energy-saving of cooling reaches 9.6%, and when the temperature is lower, the amount of iron oxide scale is significantly reduced. The benefits of low temperature rolling on the reduction of fuel consumption and iron oxide amount can completely offset and exceed the cost of increasing rolling power 。 For many rolling mills, the use of process lubrication technology can reduce the energy consumption of rolling, especially for plate mills. The hot rolling temperature of steel is generally between 800 ℃ and 1250 ℃, and the temperature of the roll surface in the deformation zone can reach 450 ℃ - 550 ℃. Therefore, a lot of water is needed to cool the roll. Through the experiment, it can be found that the consumption of rolling power decreases by about 8% due to the reduction of the rolling force.
The energy crisis is becoming more and more serious, we must pay enough attention to the use of energy-saving technology in steel rolling production. The development form of the iron and steel industry in our country urgently requires iron and steel enterprises to use the new technology of energy-saving and consumption reduction. It is necessary to increase the research on energy-saving technology and energy-saving technology in steel rolling production, increase the investment in science and technology, save resources, meet the technical needs of modern steel rolling production to the greatest extent, reduce energy consumption, save resources, and promote the sustainable development of economy and society.
Please contact
stella@hanrm.com for a quotation.
And free send inquiry to us.
Email:
stella@hanrm.com stellarollingmill@gmail.com
Whatsapp/Wechat:+8615877652925
More News You May Interesting:
Finishing Rolling Mill Process Explanation
Reasons and Solutions for the Piling of Wire Rod Rolling
Characteristics and Quality of Wire Rod
Morgan Wire Rod Mill
Why does the Steel Bar Bend after being Cut by Flying Shear?
Headless Welding Rolling Process
Bar Rolling Mills Water Cooling Technology
How to Improve the Thermal Efficiency of the Reheating Furnaces?
Causes of Surface Cracks in High-Speed Wire Rod Rolling Mill
What is Slit Rolling?
Failure Analysis of Cold Mill Roll
Causes and Solution of Steel Piling-up in High-speed Wire Rod Rolling Mills?
Bar Automatic Counting System
Rolling Mill Pass Design